Alabama Chanin Supply Chain Page
97% of clothing sold in the U.S. is made overseas. Our organic cotton is sourced, ginned, spun, knitted, and dyed in the American South before being hand-sewn by artisans in The Shoals—supporting local industry, sustainable practices, and cultural heritage.
TRANSPARENCY | SUSTAINABILITY | PRESERVATION
Cotton has been at the heart of our organization for over two decades. First in the form of recycled cotton T-shirts, and since 2005, in partnership with our Texas farmers and North Carolina converters providing a seed-to-shelf U.S.-made and organic product.
This plant, and its fiber, are rooted in the complicated history of our region. It shapes and inspires the work and informs the future of our organization: making, teaching, documenting, connecting.
MAKING
Pieces in the Alabama Chanin Collection are crafted from American-made, organic cotton jersey by a group of artisan sewers in and around The Shoals community of northwest Alabama. Every garment is made to order—a lean method manufacturing approach that allows us to make the most sustainable use of our fabric.
TEACHING
Taking fabric scraps seriously is also part of Project Threadways’ goal of becoming a zero waste organization. Zero waste education—in the style of Alabama Chanin’s Zero Waste Waffle sweatshirts—is part of all workshops held at The Factory and beyond through The School of Making.
DOCUMENTING
Project Threadways’ collection of oral history interviews features the voices of cotton farmers, factory workers, machine operators, and artisan sewers in northwest Alabama and beyond. This documentary work aims to preserve the stories of the people who have helped build the local textile industry.
Oral Histories and More Coming Soon
CONNECTING
Through the Southeast Fibershed, Project Threadways connects producers and makers across the American South, nurturing a regional supply chain to build stronger and more equitable futures. Email development@projectthreadways.org for more information.
Take a closer look at our US-grown, organic cotton supply chain below.
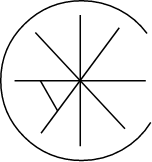
US GROWN, ORGANIC SUPPLY CHAIN

— Cotton and Farming
Since 2004, Alabama Chanin's supply chain begins at the Texas Organic Cotton Marketing Cooperative (TOCMC) in Lubbock, Texas. Today, the cooperative supports 30-35 member growers, who plant approximately 18-20,000 acres of organic and transitional cotton each year. In 2021, these acres produced around 7,000 bales of cotton. The cooperative and its members are certified organic under the United States Department of Agriculture National Organic Program.
Photo above: /Embroidery: Threads and Stories/ by Natalie Chanin, page 34-35, Cotton in the field, Northwest Alabama photographed by Robert Rausch

— Traceability
Once picked, the certified organic cotton is tracked from field-to-fabric through a barcode system that is applied to each bale in the ginning process. As a consumer, the ability to trace organic fiber back to farms and producers is ensured through the application of these barcodes.
Photo above: /Embroidery: Threads and Stories/ by Natalie Chanin, page 36, Picking organic cotton photographed by Rinne Allen
In 2020, and in the midst of Covid-19, Texas cotton growers experienced two weather events that caused the year’s supply to have a short fiber length that caused issues in the spinning, knitting, and dying process. For this reason, we looked beyond the Texas border to secure a supply for cotton jersey. For this reason, we worked with Supima cotton, grown in the states of California, Arizona, Texas and New Mexico. There are limited supplies of this cotton in our inventory

— Ginning
Once the cotton is picked and retrieved from the field, it is ginned through four gins in the vicinity of Lubbock, Texas. Through the ginning process, cotton fibers are pulled from the seeds while dirt, burs, stems, and any leaves that adhere to the fiber are removed.
Photo above: /Embroidery: Threads and Stories/ by Natalie Chanin, page 40-41, Bales of organic Alabama cotton await processing at Hill Spinning in North Carolina photographed by Rinne Allen

— Transportation
Ginned cotton is transported from Texas to spinning facilities in North Carolina for processing into yarn. While these are not certified organic facilities, they do produce to Global Organic Textile Standards. Oftentimes, processing facilities choose not to become certified due to the high cost of certification.
Photo above: /Embroidery: Threads and Stories/ by Natalie Chanin, page 42, A truck departs cotton gin photographed by Rinne Allen
Embroidery: Threads and Stories by Natalie Chanin, page 43, Detail of cotton tufts after cleaning photographed by Rinne Allen

— Spinning
Most often, a projected supply of one year of cotton is spun into yarn at the same time. This yarn will eventually become the Medium-weight Organic Cotton Jersey and Organic Waffle.
Alabama Chanin and The School of Making commit on average to 20,000 lbs per year of domestic cotton and 11,000 lbs per year of imported light-weight yarns.
Photo above: /Embroidery: Threads and Stories/ by Natalie Chanin, page 44-45, Looking up toward one of the machines at Hill Spinning photographed by Rinne Allen

— Knitting
From the spinner, the cotton moves to South Carolina, where it is received by a fourth-generation, family-owned and operated company that has been in operation since 1938. It is here the fiber is knit into fabric.
Embroidery: Threads and Stories by Natalie Chanin, page 46, Rolls of organic cotton being spun into thread at Professional Knitters in South Carolina photographed by Rinne Allen
Embroidery: Threads and Stories by Natalie Chanin, page 47, Embroidered garments, Alabama Chanin, photographed by Rinne Allen

— Dyeing
Once the cotton has become fabric it is dyed in South Carolina, using low impact, cold process, environmentally friendly dyes. Once the fabric is dyed, it is shipped to Florence, Alabama, where it creates Alabama Chanin’s products.
Photo above: /Embroidery: Threads and Stories/ by Natalie Chanin, page 198-199, Fabric Swatch #24386, Alabama Chanin, photographed by Abraham Rowe

— Local Manufacturing
Building 14 machine manufacturing, officially born in 2013, is a natural expansion of our hand-sewn ethos and part of the Alabama Chanin. The concept is inspired by our community’s history of manufacturing, led by companies like t-shirt manufacturer Tee Jays and others which, throughout the 1970s, 80s, and 90s, employed thousands in our region. As those companies were forced to close as a result of the NAFTA legislation, an entire skillset began to fade away, and we wanted to both honor those skills and adapt them for the future.
Tee Jays is well-known in our community for creating a family atmosphere and that is something we always aspire to at Alabama Chanin. The building where the entirety of The Factory lives was once part of the Tee Jays facility (their plant #14) – one of the largest, thriving manufacturing locations in the region. It is an honor for us to turn the machines on each morning and hear their productive humming.
Photo above: /Embroidery: Threads and Stories/ by Natalie Chanin, page 48-49, Organic fabric awaits cutting, Building 14, Alabama Chanin, photographed by Rinne Allen
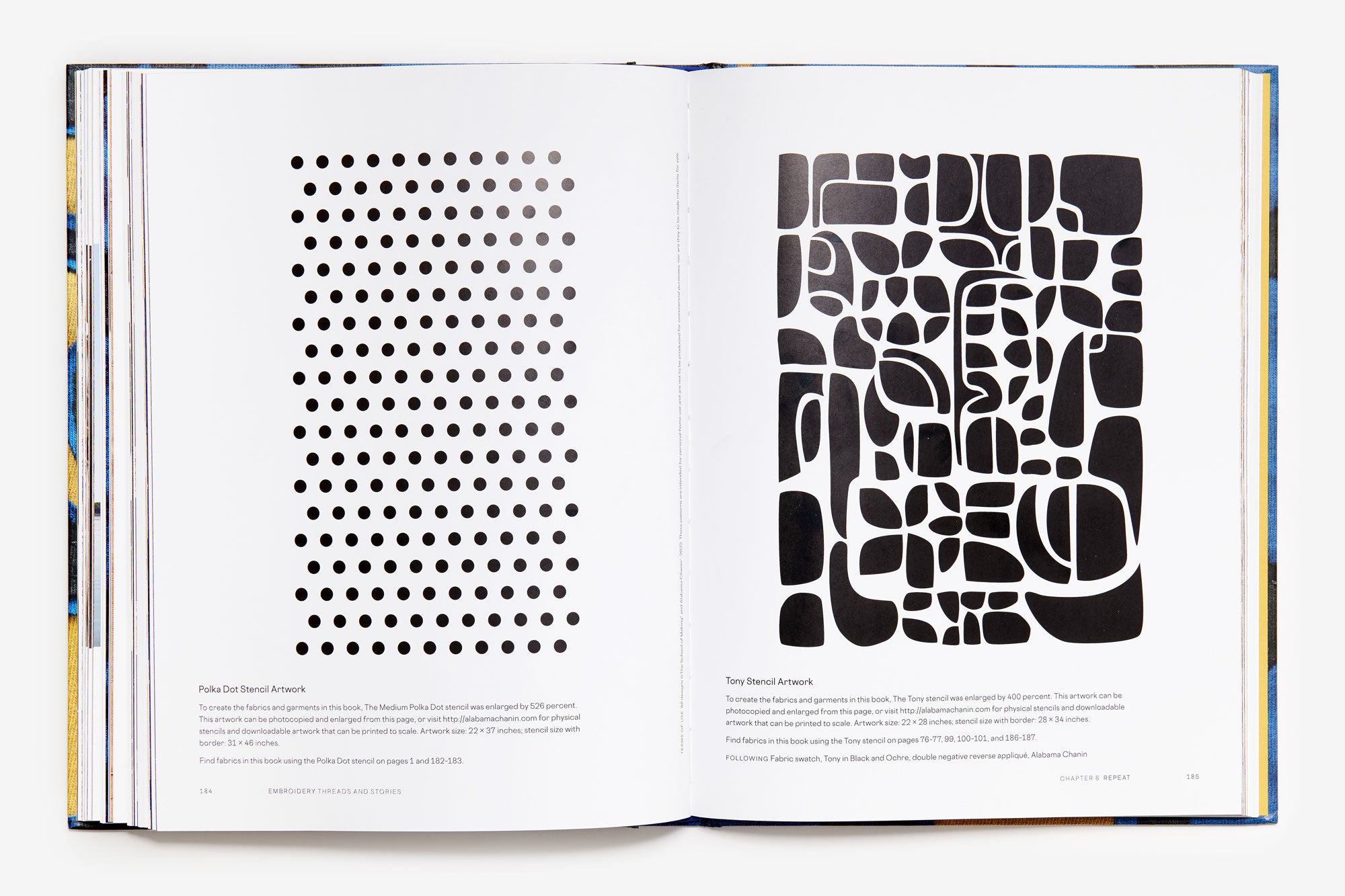
— Stencils and Lean Method Manufacturing
For two decades, we have carefully balanced our supply chain with lean method manufacturing to produce each piece one at a time, made to order. This ensures we deliver the best possible product to our guests and utilize our raw materials in the most sustainable and effective way.
Photo above: /Embroidery: Threads and Stories/ by Natalie Chanin, page 184-185, the Polka Dot Stencil and Tony Stencil designs photographed by Robert Rausch

— Seed to Shelf
In addition to our part- and full-time employees at The Factory (including our store, production, design, media, education and workshops teams, and Building 14 machine manufacturing), we work with artisans in the surrounding communities in northern Alabama and southern Tennessee. Each of these people must work seamlessly with the next in order for fabric to be cut and painted, then either hand sewn by artisans or machine sewn in Bldg. 14 before it arrives at its new home.
Photo above: /Embroidery: Threads and Stories/ by Natalie Chanin, page 218, The Rosanne Coat, Alabama Chanin, photographed by Abraham Rowe

— Cotton and Farming
Since 2004, Alabama Chanin's supply chain begins at the Texas Organic Cotton Marketing Cooperative (TOCMC) in Lubbock, Texas. Today, the cooperative supports 30-35 member growers, who plant approximately 18-20,000 acres of organic and transitional cotton each year. In 2021, these acres produced around 7,000 bales of cotton. The cooperative and its members are certified organic under the United States Department of Agriculture National Organic Program.
Photo above: /Embroidery: Threads and Stories/ by Natalie Chanin, page 34-35, Cotton in the field, Northwest Alabama photographed by Robert Rausch

— Traceability
Once picked, the certified organic cotton is tracked from field-to-fabric through a barcode system that is applied to each bale in the ginning process. As a consumer, the ability to trace organic fiber back to farms and producers is ensured through the application of these barcodes.
Photo above: /Embroidery: Threads and Stories/ by Natalie Chanin, page 36, Picking organic cotton photographed by Rinne Allen
In 2020, and in the midst of Covid-19, Texas cotton growers experienced two weather events that caused the year’s supply to have a short fiber length that caused issues in the spinning, knitting, and dying process. For this reason, we looked beyond the Texas border to secure a supply for cotton jersey. For this reason, we worked with Supima cotton, grown in the states of California, Arizona, Texas and New Mexico. There are limited supplies of this cotton in our inventory

— Ginning
Once the cotton is picked and retrieved from the field, it is ginned through four gins in the vicinity of Lubbock, Texas. Through the ginning process, cotton fibers are pulled from the seeds while dirt, burs, stems, and any leaves that adhere to the fiber are removed.
Photo above: /Embroidery: Threads and Stories/ by Natalie Chanin, page 40-41, Bales of organic Alabama cotton await processing at Hill Spinning in North Carolina photographed by Rinne Allen

— Transportation
Ginned cotton is transported from Texas to spinning facilities in North Carolina for processing into yarn. While these are not certified organic facilities, they do produce to Global Organic Textile Standards. Oftentimes, processing facilities choose not to become certified due to the high cost of certification.
Photo above: /Embroidery: Threads and Stories/ by Natalie Chanin, page 42, A truck departs cotton gin photographed by Rinne Allen
Embroidery: Threads and Stories by Natalie Chanin, page 43, Detail of cotton tufts after cleaning photographed by Rinne Allen

— Spinning
Most often, a projected supply of one year of cotton is spun into yarn at the same time. This yarn will eventually become the Medium-weight Organic Cotton Jersey and Organic Waffle.
Alabama Chanin and The School of Making commit on average to 20,000 lbs per year of domestic cotton and 11,000 lbs per year of imported light-weight yarns.
Photo above: /Embroidery: Threads and Stories/ by Natalie Chanin, page 44-45, Looking up toward one of the machines at Hill Spinning photographed by Rinne Allen

— Knitting
From the spinner, the cotton moves to South Carolina, where it is received by a fourth-generation, family-owned and operated company that has been in operation since 1938. It is here the fiber is knit into fabric.
Embroidery: Threads and Stories by Natalie Chanin, page 46, Rolls of organic cotton being spun into thread at Professional Knitters in South Carolina photographed by Rinne Allen
Embroidery: Threads and Stories by Natalie Chanin, page 47, Embroidered garments, Alabama Chanin, photographed by Rinne Allen

— Dyeing
Once the cotton has become fabric it is dyed in South Carolina, using low impact, cold process, environmentally friendly dyes. Once the fabric is dyed, it is shipped to Florence, Alabama, where it creates Alabama Chanin’s products.
Photo above: /Embroidery: Threads and Stories/ by Natalie Chanin, page 198-199, Fabric Swatch #24386, Alabama Chanin, photographed by Abraham Rowe

— Local Manufacturing
Building 14 machine manufacturing, officially born in 2013, is a natural expansion of our hand-sewn ethos and part of the Alabama Chanin. The concept is inspired by our community’s history of manufacturing, led by companies like t-shirt manufacturer Tee Jays and others which, throughout the 1970s, 80s, and 90s, employed thousands in our region. As those companies were forced to close as a result of the NAFTA legislation, an entire skillset began to fade away, and we wanted to both honor those skills and adapt them for the future.
Tee Jays is well-known in our community for creating a family atmosphere and that is something we always aspire to at Alabama Chanin. The building where the entirety of The Factory lives was once part of the Tee Jays facility (their plant #14) – one of the largest, thriving manufacturing locations in the region. It is an honor for us to turn the machines on each morning and hear their productive humming.
Photo above: /Embroidery: Threads and Stories/ by Natalie Chanin, page 48-49, Organic fabric awaits cutting, Building 14, Alabama Chanin, photographed by Rinne Allen
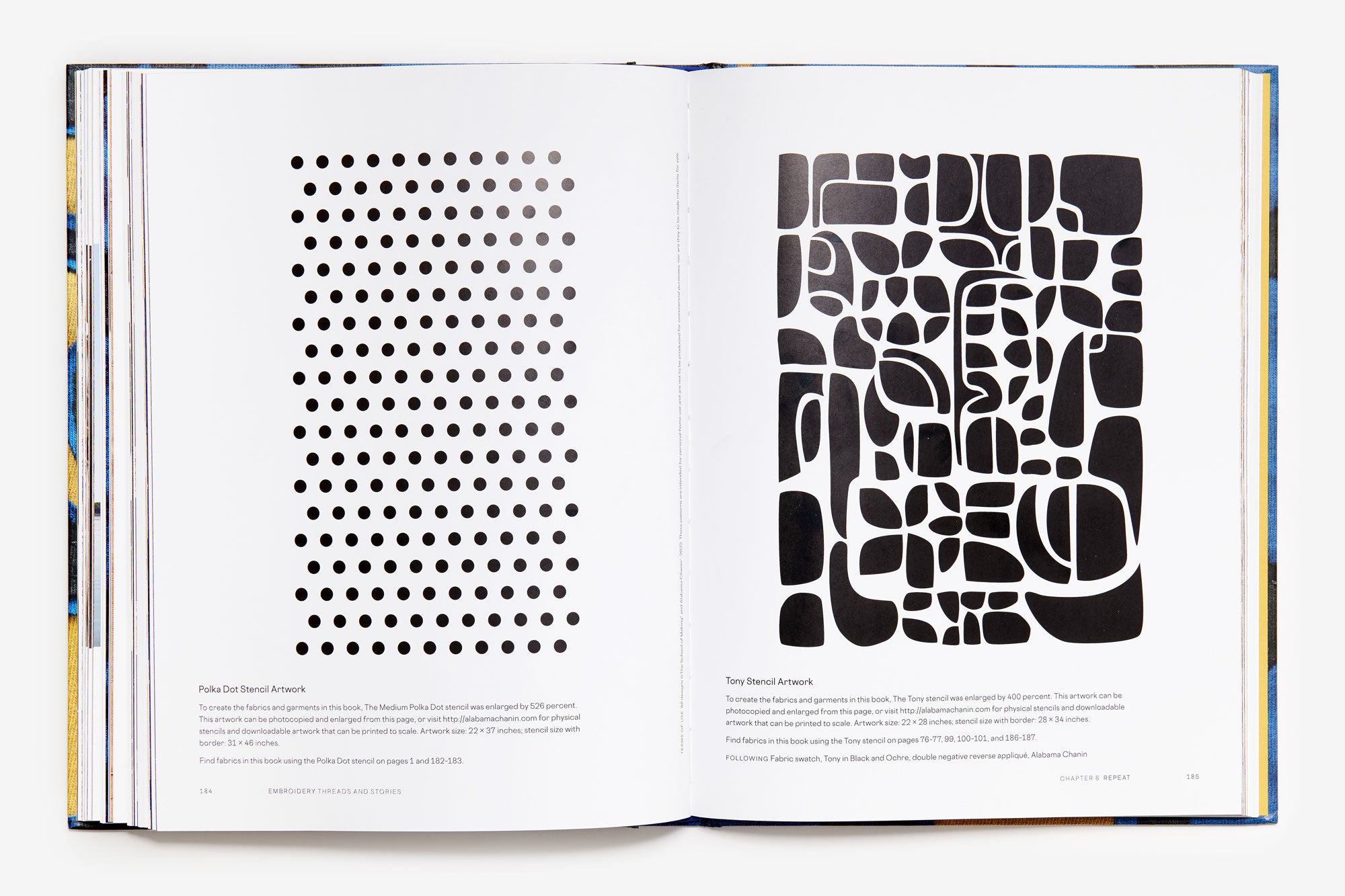
— Stencils and Lean Method Manufacturing
For two decades, we have carefully balanced our supply chain with lean method manufacturing to produce each piece one at a time, made to order. This ensures we deliver the best possible product to our guests and utilize our raw materials in the most sustainable and effective way.
Photo above: /Embroidery: Threads and Stories/ by Natalie Chanin, page 184-185, the Polka Dot Stencil and Tony Stencil designs photographed by Robert Rausch

— Seed to Shelf
In addition to our part- and full-time employees at The Factory (including our store, production, design, media, education and workshops teams, and Building 14 machine manufacturing), we work with artisans in the surrounding communities in northern Alabama and southern Tennessee. Each of these people must work seamlessly with the next in order for fabric to be cut and painted, then either hand sewn by artisans or machine sewn in Bldg. 14 before it arrives at its new home.
Photo above: /Embroidery: Threads and Stories/ by Natalie Chanin, page 218, The Rosanne Coat, Alabama Chanin, photographed by Abraham Rowe

— Cotton and Farming
Since 2004, Alabama Chanin's supply chain begins at the Texas Organic Cotton Marketing Cooperative (TOCMC) in Lubbock, Texas. Today, the cooperative supports 30-35 member growers, who plant approximately 18-20,000 acres of organic and transitional cotton each year. In 2021, these acres produced around 7,000 bales of cotton. The cooperative and its members are certified organic under the United States Department of Agriculture National Organic Program.
Photo above: /Embroidery: Threads and Stories/ by Natalie Chanin, page 34-35, Cotton in the field, Northwest Alabama photographed by Robert Rausch

— Traceability
Once picked, the certified organic cotton is tracked from field-to-fabric through a barcode system that is applied to each bale in the ginning process. As a consumer, the ability to trace organic fiber back to farms and producers is ensured through the application of these barcodes.
Photo above: /Embroidery: Threads and Stories/ by Natalie Chanin, page 36, Picking organic cotton photographed by Rinne Allen
In 2020, and in the midst of Covid-19, Texas cotton growers experienced two weather events that caused the year’s supply to have a short fiber length that caused issues in the spinning, knitting, and dying process. For this reason, we looked beyond the Texas border to secure a supply for cotton jersey. For this reason, we worked with Supima cotton, grown in the states of California, Arizona, Texas and New Mexico. There are limited supplies of this cotton in our inventory

— Ginning
Once the cotton is picked and retrieved from the field, it is ginned through four gins in the vicinity of Lubbock, Texas. Through the ginning process, cotton fibers are pulled from the seeds while dirt, burs, stems, and any leaves that adhere to the fiber are removed.
Photo above: /Embroidery: Threads and Stories/ by Natalie Chanin, page 40-41, Bales of organic Alabama cotton await processing at Hill Spinning in North Carolina photographed by Rinne Allen

— Transportation
Ginned cotton is transported from Texas to spinning facilities in North Carolina for processing into yarn. While these are not certified organic facilities, they do produce to Global Organic Textile Standards. Oftentimes, processing facilities choose not to become certified due to the high cost of certification.
Photo above: /Embroidery: Threads and Stories/ by Natalie Chanin, page 42, A truck departs cotton gin photographed by Rinne Allen
Embroidery: Threads and Stories by Natalie Chanin, page 43, Detail of cotton tufts after cleaning photographed by Rinne Allen

— Spinning
Most often, a projected supply of one year of cotton is spun into yarn at the same time. This yarn will eventually become the Medium-weight Organic Cotton Jersey and Organic Waffle.
Alabama Chanin and The School of Making commit on average to 20,000 lbs per year of domestic cotton and 11,000 lbs per year of imported light-weight yarns.
Photo above: /Embroidery: Threads and Stories/ by Natalie Chanin, page 44-45, Looking up toward one of the machines at Hill Spinning photographed by Rinne Allen

— Knitting
From the spinner, the cotton moves to South Carolina, where it is received by a fourth-generation, family-owned and operated company that has been in operation since 1938. It is here the fiber is knit into fabric.
Embroidery: Threads and Stories by Natalie Chanin, page 46, Rolls of organic cotton being spun into thread at Professional Knitters in South Carolina photographed by Rinne Allen
Embroidery: Threads and Stories by Natalie Chanin, page 47, Embroidered garments, Alabama Chanin, photographed by Rinne Allen

— Dyeing
Once the cotton has become fabric it is dyed in South Carolina, using low impact, cold process, environmentally friendly dyes. Once the fabric is dyed, it is shipped to Florence, Alabama, where it creates Alabama Chanin’s products.
Photo above: /Embroidery: Threads and Stories/ by Natalie Chanin, page 198-199, Fabric Swatch #24386, Alabama Chanin, photographed by Abraham Rowe

— Local Manufacturing
Building 14 machine manufacturing, officially born in 2013, is a natural expansion of our hand-sewn ethos and part of the Alabama Chanin. The concept is inspired by our community’s history of manufacturing, led by companies like t-shirt manufacturer Tee Jays and others which, throughout the 1970s, 80s, and 90s, employed thousands in our region. As those companies were forced to close as a result of the NAFTA legislation, an entire skillset began to fade away, and we wanted to both honor those skills and adapt them for the future.
Tee Jays is well-known in our community for creating a family atmosphere and that is something we always aspire to at Alabama Chanin. The building where the entirety of The Factory lives was once part of the Tee Jays facility (their plant #14) – one of the largest, thriving manufacturing locations in the region. It is an honor for us to turn the machines on each morning and hear their productive humming.
Photo above: /Embroidery: Threads and Stories/ by Natalie Chanin, page 48-49, Organic fabric awaits cutting, Building 14, Alabama Chanin, photographed by Rinne Allen
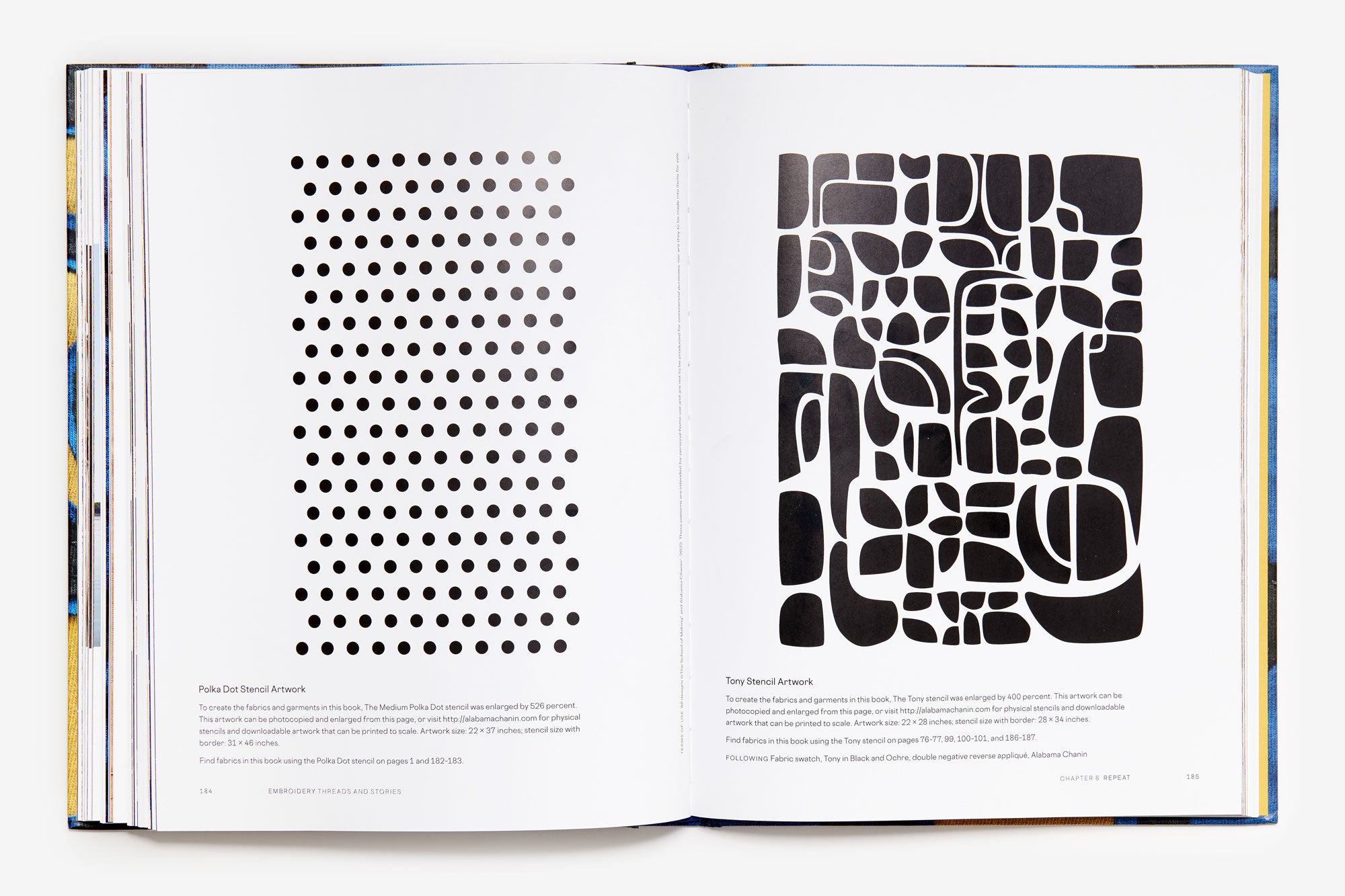
— Stencils and Lean Method Manufacturing
For two decades, we have carefully balanced our supply chain with lean method manufacturing to produce each piece one at a time, made to order. This ensures we deliver the best possible product to our guests and utilize our raw materials in the most sustainable and effective way.
Photo above: /Embroidery: Threads and Stories/ by Natalie Chanin, page 184-185, the Polka Dot Stencil and Tony Stencil designs photographed by Robert Rausch

— Seed to Shelf
In addition to our part- and full-time employees at The Factory (including our store, production, design, media, education and workshops teams, and Building 14 machine manufacturing), we work with artisans in the surrounding communities in northern Alabama and southern Tennessee. Each of these people must work seamlessly with the next in order for fabric to be cut and painted, then either hand sewn by artisans or machine sewn in Bldg. 14 before it arrives at its new home.
Photo above: /Embroidery: Threads and Stories/ by Natalie Chanin, page 218, The Rosanne Coat, Alabama Chanin, photographed by Abraham Rowe

Mission-Driven
Community-Led
PROJECT THREADWAYS